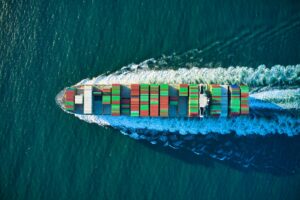
Since the onset of the pandemic, global supply chains have suffered unprecedented disruptions. Volatility in supply and demand, as well as route restrictions, have caused catastrophic breakdowns. Critical supply chains that should be resilient with ample redundancy built in have instead been revealed to be highly vulnerable.
A Dun & Bradstreet study found that 163 Fortune 1000 companies had Tier 1 suppliers impacted and 938 had Tier 2 supplier impacted by the pandemic. According to Capgemini research, 74% of supply chain companies faced a shortage of critical parts and materials, and 68% had products held up in ports or across borders.
Similarly in Australia, according the Australian Bureau of Statistics (ABS), over a third (37 per cent) of all businesses experienced supply chain disruptions in February 2022.
The survey found the most common supply chain issue facing businesses was domestic and international delivery delays (88 per cent), while 80 per cent had supply constraints and 75 per cent had seen increased prices (including transport costs).
A key reason is the vast complexity of global supply chains. With so many different links in terms of sources, suppliers and routes they are highly multi-dimensional, making it extremely difficult to get visibility through traditional methods. Without visibility, it’s very hard to find redundancies in terms of alternate routes and suppliers.
The need for supply chain visibility
To be resilient, supply chains need to be visible. As McKinsey notes, one way to build long-term supply chain resilience is to construct a digital twin: “a virtual replica of a business’s operation that allows companies to simulate how a product, process, or service will perform before it is implemented in the real world.”
Essentially, supply chains are all about understanding networks and dependencies. So, data that’s usually in different data stores, such as demand, supply, manufacturing, warehousing, and transportation, all needs to be combined in a seamless way to harness the inherent relationships.
This is where knowledge graphs can help alleviate the supply chain issue as they bridge data silos and create a connected supply chain that allows companies to better manage, analyse and visualise their data by providing a trackable and in-depth picture of all products, suppliers and facilities and the relationships between them.
Knowledge graphs can be used to carry out various kinds of analysis, such as ‘What If’ or ‘Impact’ analysis. This ranges from specific questions such as:“How many assemblies depend on a product, and what happens if that goes down? How many downstream processes are affected?” to broader queries such as: “What are the points of failure in our network, and what is the impact of that failure?”
Harnessing graph technology in a Bill of Materials use case
A Bill of Materials (BOM) which is the blueprint of a product, is a comprehensive inventory of the raw materials, assemblies, sub-assemblies, parts, components, and quantities of each material and their sources; is the perfect example of a graph use case because there are so many dependencies amongst components, parts, suppliers, costs, delivery shipping and so on.
Many organisations are still using traditional Product Lifecycle Management (PLM) systems, and even just Excel spreadsheets, to manage the Bill of Materials. However, these solutions can no longer manage the complexity nor offer the visibility required and don’t go far enough in answering critical BOM questions.
In contrast, the data structure of a knowledge graph is ideal for storing supply chain data, scaling to billions of nodes and relationships. It provides a holistic, 360-degree view and enables smarter, more predictive decision-making. A simple graph query can be carried out for a question such as: “What are all the components that are shared by Model X and Model Y and are used in production in our Hungary plant?”
Or by using graph analytics algorithms, queries can be made such as: “If my tier one supplier for component x is impacted, are there are other suppliers that I can get this component from?” or “If the component inventory runs low or supply is disrupted, can I find a similar component to replace?”
An example of a company using graph technology is Murrelektronik which provides decentralised automation technology for machines and plants. It has created a Product Information Management (PIM) Knowledge Graph for 60,000 products, which involves 62 million nodes and 95 million relationships.
Users can easily navigate the graph and actively collaborate, from technicians and product managers to test centre and quality control to marketing. Murrelektronik can also create specific reports for major customers that provide a very fine-grained overview of products.
According to Deloitte, 79% of companies with a robust and high-performing supply chain outperform their average peers in terms of higher revenue growth.
For companies to ensure that they have greater visibility to their supply chain so that they can make more informed decisions, using knowledge graphs can help identify risks by tracking multi-tiered supplier information, costs, and disruptions so that companies can take corrective action before shortages impact business operations.
By Dr. Maya Natarajan, Senior Director, Knowledge Graphs, Neo4j
This article was first published by Australian Manufacturing News