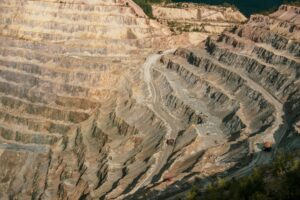
According to McKinsey, the mining sector is responsible for 4% to 7% of greenhouse gas emissions globally. Yet, the world’s demand for mining is greater than ever to meet the 2050 Net Zero goals.
The International Energy Agency (EA) observes that clean energy technologies “generally require more minerals to build than their fossil fuel-based counterparts”. The transition away from fossil fuel, needing conversion of large-scale energy systems to electrical power, will require mining two times more copper over the next decade, from 25 million metric tons today to about 50 million metric tons by 2035, according to S&P Global.
Mine operators face a triple challenge. They need to increase output while simultaneously decreasing their emissions. At the same time, they battle rising costs, from energy costs to rapidly falling ore grades that require more material to be moved and more rock to be crushed. To be more sustainable, productive and cost-efficient, it’s clear that mining needs to be done differently in future.
Other sectors facing these challenges have adopted a range of pathways. For example, the power sector has shifted towards renewable energy and energy storage solutions. There’s been a focus on waste reduction and resource efficiency with product lifecycle management in manufacturing.
The most relevant innovations for mining stem from the electric vehicle and tech sectors. In the immediate term, advances in cloud computing and artificial intelligence (Al) have the potential to significantly reduce emissions in mining by optimising operations to deliver maximum output without additional costs, reducing fuel burn, and extending the life of consumables (such as tyres). Major equipment changes, in the form of electrification of mobile machinery, are still years away from commercialisation.
Dealing with the diesel dilemma
Diesel-powered equipment is a major contributor to mining emissions. The average mine site has a fleet of around forty trucks and excavators, generating around 150,000 tonnes of carbon a year. Reducing these diesel emissions is critical to meeting net zero goals, but we have yet to see zero or even low-emissions machines gain traction in commercial operations.
Some companies such as Fortescue and Anglo-American are conducting battery and hydrogen-powered mining haul truck trials.
However, these technologies still need to be proven and remain far from mainstream adoption. Another barrier that will slow adoption is the higher capital cost of electric vehicles than their diesel counterparts.
One option that could make a significant difference now is unlocking the power of data with Al. Using existing data analytics technology, mine fleets could be operated more efficiently, with maximised payloads, reduced downtime, and safer and more efficient driving – leading to an increase in sustainability. Data collected from mobile mining equipment can be augmented and analysed to contextualise what the asset was doing at every moment, providing crystal clear visibility of load and haul productivity across the entire operation.
Insights can then be generated to determine the best optimisations to make to improve operational efficiency and reduce diesel use: from the right gear choice to optimise truck efficiency, the best speed on each road section to safely optimise cycle times and tonnes moved, and improving fill factor to maximise payloads without damaging trucks. It’s similar to the feedback a Formula One race driver receives on every lap of the course. Simply by
optimising diesel trucks, the average open pit mine could cut 5-15% of its on-site emissions, reducing its carbon footprint by about 30,000 tonnes of CO2. Combining best practices and current commercialised technologies, including electric excavators, mines could target emission reduction of up to 40% in the near term.
Cutting carbon at Karara
NRW Civil & Mining, one of Australia’s leading contractors, is partnering with MaxMine to reduce greenhouse gas emissions at the Karara Iron Ore project, the largest mining operation in Western Australia’s Mid-West region. NRW is responsible for extracting ore and waste, managing haulage, and loading trains.
NRW wanted to deploy an intelligent technology solution at Karara to harness data-driven insights to refine operator behaviours, improve performance, and establish tangible carbon emissions reduction strategies. Unlike traditional fleet management solutions, MaxMine’s platform offers granular details of what every piece of mining equipment is doing at any given moment.
MaxMine Improvement Coaches and data scientists work closely with Karara staff, using data pulled into MaxMine’s software that comes from MaxMine’s proprietary hardware installed directly on the asset, to optimise efficiency and promote environmentally sustainable practices. MaxMine also provides tailored reports that are sent to production management and Mine Control every day, as well as screens for the front line teams to provide them with near real-time insights about performance. Additionally, operators are able to see how they are travelling through the phone-based application that displays individual performance vs. agreed targets to encourage self-learning and improvement.
NRW’s main objective was to enhance operator behaviour and ensure each operator maintained optimal travel speeds to maximise safety and productivity while reducing road degradation and overall carbon footprint.
Initially, ramp, zone, and corner speeds were targeted. Expectations were set and crews were coached on how to meet them. The solution also provided personalised performance feedback to individual operators, displayed as a league table to encourage healthy competition. Every day, operators could refine their practices based on near-real-time data.
This improved NRW’s overall operator performance scores from a baseline of 72% to 96%, ensuring that all operators are consistently meeting clearly defined operating standards. The average fill factor also increased to three extra tons per load. With approximately 17,000 loads monthly, this translates to an additional 612,000 tons of material being moved annually without incurring any extra costs.
Advanced technologies such as Al hold huge potential for the mining sector, but industry collaboration is key to achieving net zero. MaxMine’s #first40 initiative collaborates with mining companies to reduce emissions on mine sites by 40 percent using data and analytics, and the integration of existing technologies such as electric hydraulic phase shovels and low-carbon diesels.
The mining industry’s role in enabling a net zero future is undeniable, but its practices must evolve to sustainably meet the growing demand for minerals. By embracing advanced technologies, alongside industry-wide collaboration, and a commitment to reducing emissions, mining can become not only more productive but also a significant player in the global effort to combat climate change.
By Tom Cawley, Executive Chair and Interim CEO, MaxMine
This article was first published by Australian Manufacturing Tech Magazine